Freeze Seals
It is common knowledge that freezing water can fracture pipes; however, did you know it can also save the day?
Here’s the situation:
You’re in charge of a large industrial facility and have discovered a machine in critical need of repair. The repair requires that the machine’s cooling piping be isolated and drained. Unfortunately, the machine’s cooling piping is part of a network of piping and heat exchangers that also provide cooling to the rest of your facility’s equipment. You have a limited number of valves that can be shut and aren’t sure if they’re “leak tight”. Replacing these valves or adding more valves would require the same shutdown that you’re already looking at and trying to avoid. A full repair would take five days; however, you can only shutdown your operations overnight without affecting your bottom line.
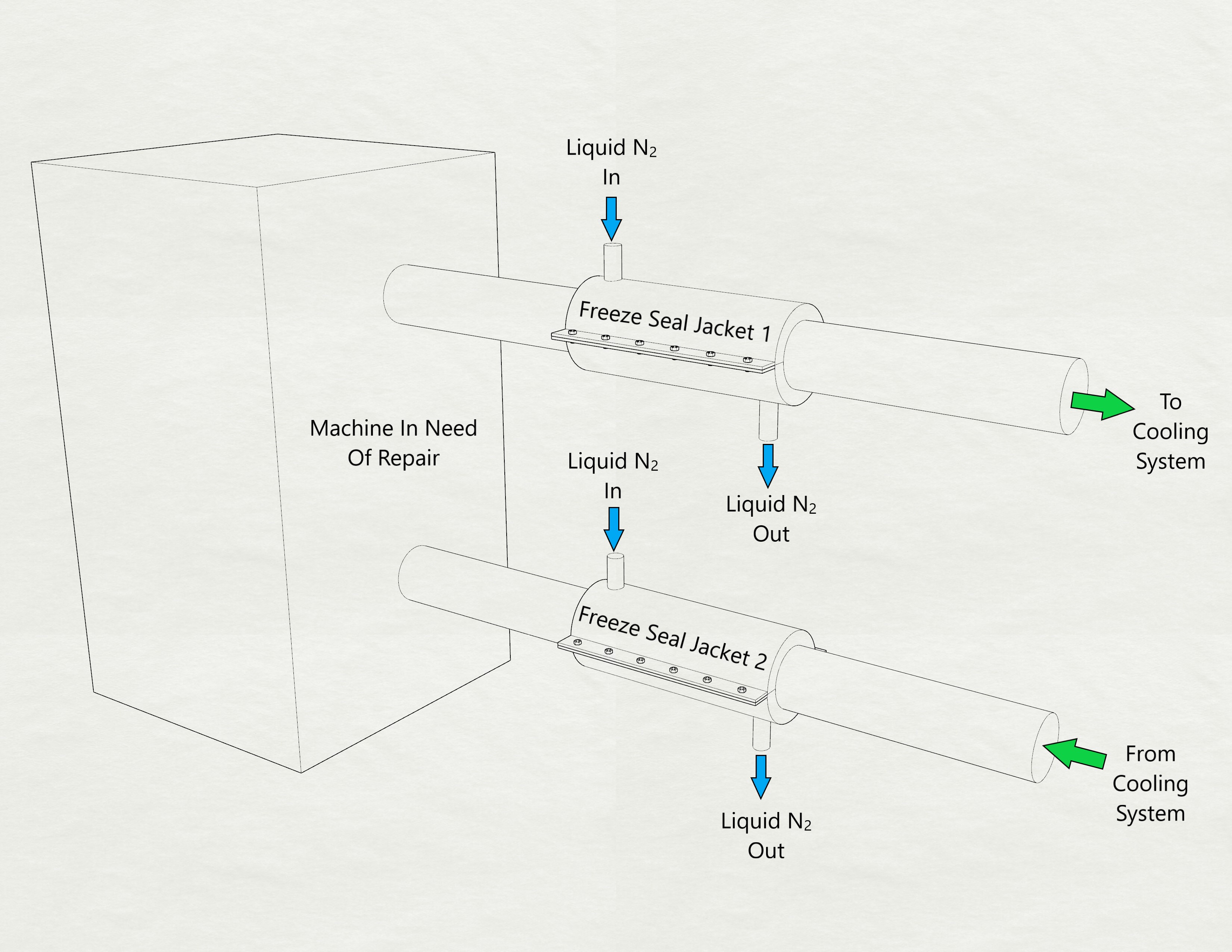
What do you do?
Cue the freeze seal.
Utilized in nuclear power plants and other facilities on a regular basis, a freeze seal consists of an intentional mass of ice within a pipe that prevents water movement similar to a shut valve. With proper planning and operation, a freeze seal is capable of holding back thousands of pounds of pressure. This holding power comes from a combination of surface adhesion, friction, and localized temporary deformation of the pipe.

Multiple methods exist to create freeze seals including, pumping liquid nitrogen through a jacket wrapped around a pipe or supplying a vortex cooled air stream (a topic for another day) into a similar jacket around the pipe. In each method, a section of pipe—often a long straight section—is chosen and equipment selected to generate adequate cooling. Temperature monitoring is put in place, flow through the pipe is stopped, and cooling of the freeze seal begins. The water near the walls of the pipe freezes first. Next, the freeze front progresses inwards until a solid plug of ice exists. The freeze seal is then subcooled to a pre-determined temperature at which point the freeze is considered equivalent to a shut valve (established).
With careful temperature monitoring in place and backup cooling methods at the ready, work can commence. Coolant flow throughout the rest of the system can now be restored. Following the repair, flow will again be secured for several hours while the freeze seal is given time to melt. This ensures that a slug of ice is not shot through the now repaired machine.