Hydroelectric Dams
Hydroelectric Dams
A while back, I was lucky enough to drive the full length of the Columbia River Gorge on a crisp spring morning. For those of you not familiar with this iconic geographical area, it is beyond bucket list worthy. Cut into the Cascade Mountains by the Columbia River and located just east of Portland, Oregon, this gorge has some of the best the Pacific Northwest has to offer. Grand landscape views, amazing hiking trails, camping, and biking await you at numerous locations on both sides of a hundred-mile stretch of the river. Just as impressive, this stretch of river includes three massive hydroelectric dams (Bonneville Dam, The Dalles Dam, and John Day Dam), which surprise you not only in their scale, but in how they fit into the area’s natural beauty.
How much Electricity Do Dams Generate?
According to a February 2019 U.S. Energy Information Administration (EIA) article, the total U.S. hydroelectric capacity is nearly 80,000 Megawatts. Combined, Bonneville Dam, The Dalles Dam, and John Day Dam generate 5,478 Megawatts. Assuming an average consumption rate of 1.25 KW per household, these three dams produce enough energy to power 4.4 million homes.
It is interesting to note that a large portion of dams in existence today were not built for electrical production but instead for irrigation and flood control. A 2012 U.S. EIA study found that over 12,000 Megawatts of untapped potential hydroelectric energy exists in these installations. Current planned projects will bring online 330 Megawatts of this untapped renewable energy.1
How is Electricity Generated?
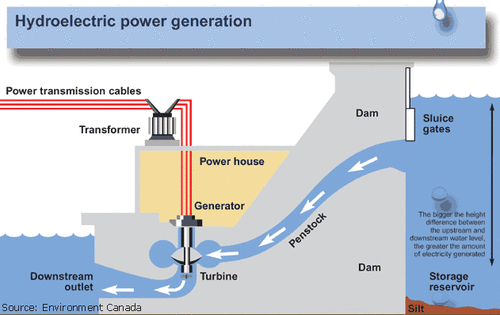
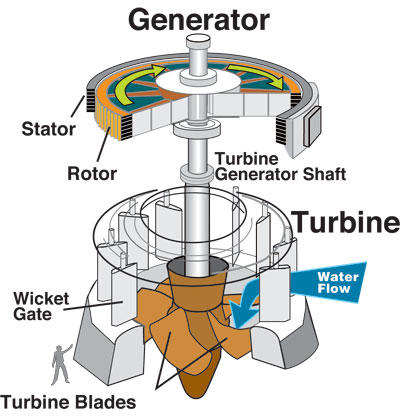
The basic concept of how hydroelectric dams generate electricity is quite simple. Water moving past a turbine results in rotation of the turbine, which is then translated to an electrical generator via a common shaft. Of course, the type, size, and quantity of turbines/generators vary considerably. Smaller hydroelectric dams may have a single turbine generator whereas larger dams may have upwards of a couple of dozen. For reference, Bonneville Dam has 20, The Dalles Dam has 22, and John Day Dam has 16.
Regardless of the size of the dam, water stored behind the dam is directed to the turbine via a tube known as a penstock. From there the water path is dependent on the type of turbine used. One common configuration utilizes what is known as a Kaplan turbine. In this configuration, water from the penstock is delivered to the turbine via a radial set of adjustable wicket gates. Water flows from these wicket gates over large adjustable pitch turbine blades and then out a draft tube towards the downstream side of the dam. Hydraulic systems are used to adjust the position of the wicket gates and turbine blades allowing this type of turbine to capture as much as 90% of the available energy.
How do you keep water out of the people's spaces?
As discussed, rotation of the turbine is translated to a generator via a common shaft. What you may be surprised to learn is that the generator(s) are not surrounded by water, and this isn’t because the generators are above the upstream water level. In fact, in most cases, they are located as low as possible. The challenge, much like a submarine’s propeller shaft, is how to keep pressurized water from moving past a spinning shaft? Remember, the goal is to prevent water from getting past the seal and to allow the shaft to spin freely. Interesting design challenge, right?
One approach is to use sealing material (packing) that is pressed against the circumference of the shaft in a specific location. A metered amount of water is then allowed to leak past the packing after which it is collected. This metered leak rate provides lubrication and cooling to the shaft as well as the packing. The rate of leakage is monitored and as it increases (packing has worn down some) bolts that clamp down on the packing can be tightened to reestablish the correct packing pressure on the spinning shaft.
What can break?
Similar to any power generation facility, just about anything can break. This is by no means a negative, but instead just an understood reality of any complex system. I’ve examined anything from defective repairs that resulted in short term breakdowns to inadequate long-term maintenance that resulted in the failure of a turbine seal. When examining these types of equipment, the amount of data available and interconnectivity often mandates a holistic approach to determining the root cause. We specialize in this kind of approach. If you ever have a question, feel free to give us a call. Hopefully, we will leave you as impressed as the fish sounded when he ran into the wall.
About the Author
David J. Shamrell, P.E. is a consulting engineer with our Seattle-Tacoma Office. Mr. Shamrell provides consultation in the areas of mechanical system investigation and analysis, damage assessment, failure analysis, and fire origin and cause analysis. You may contact David for your forensic engineering needs at dshamrell@edtengineers.com or (253) 345-5187.
Learn about how EDT Forensic Engineering & Consulting approaches fire and explosion analysis, scope of damage, and forensic engineering by assigning a file today.