A Balancing Act, Part 2 – Vibration Analysis of Structures
In Part 1 of this blog series, the effects of unbalanced loads on rotating machinery and the means a professional has to determine the cause of those effects were discussed. In this blog, a different type of vibration will be discussed – the mass-spring relationship of equipment on a foundation. In the previous blog, the discussion centered on a non-uniform weight spinning on an axis – rotational imbalance – which is excited by the spinning of the mass. For this blog, the weight is not necessarily non-uniform or off-center – it is a mass mounted on a structure, where the structure is excited by internal or external forces. Let’s look at an example – a traffic light in a storm.
Presume the traffic light is mounted on a boom off a pole – like Figure 1. The light itself has mass, and it is offset from the center of the pole. Add some wind, and the light acts like a sail – what a driver will see is the light swaying and bouncing. This is not because the light is dangling from the pole – it’s because the excitation from the force generated by the wind on the light coincides with the harmonic frequencies of the pole in bending and twisting.
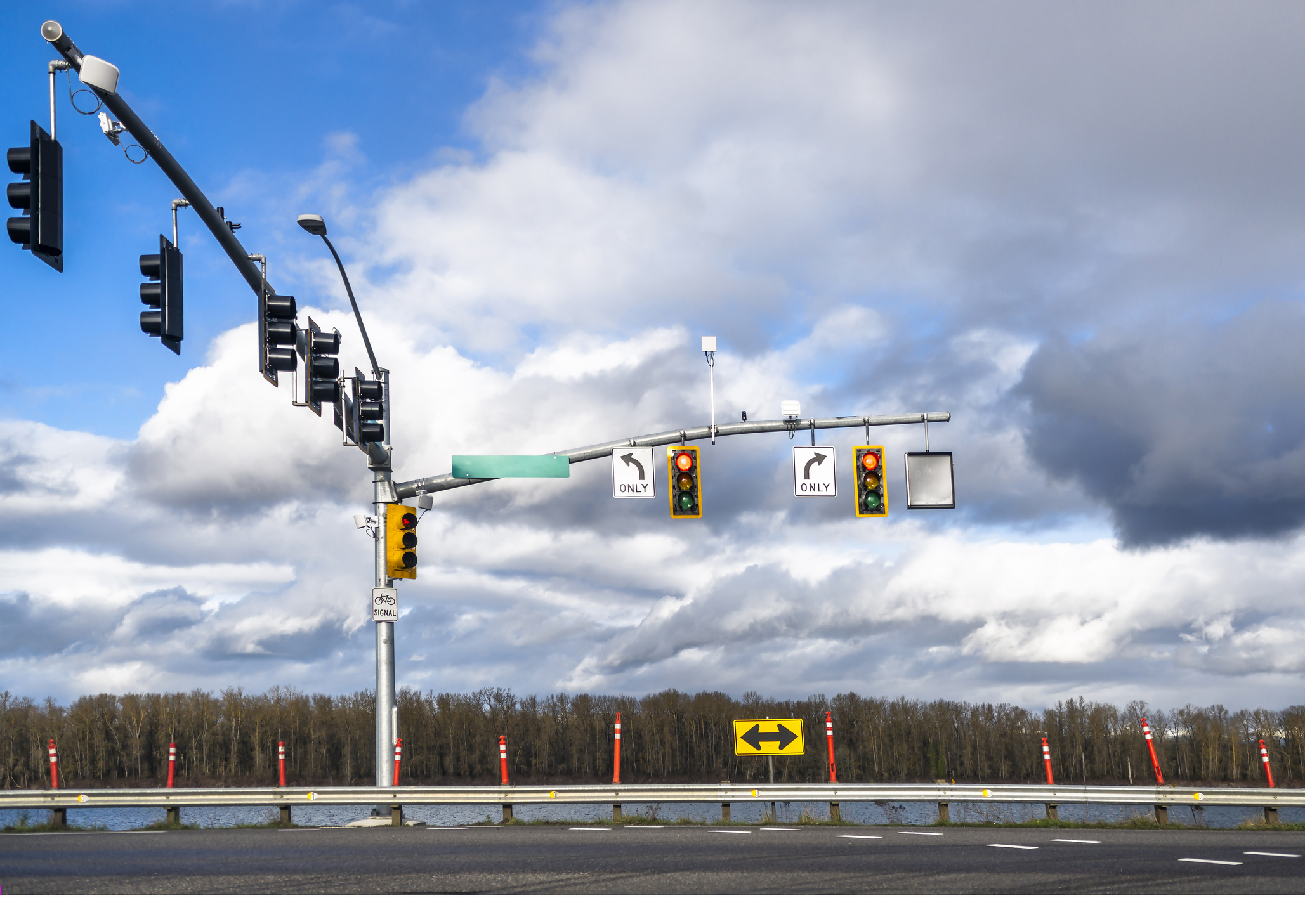
The traffic light is just a very visible example of a common phenomenon with nearly any structure – vibration response of a mass-spring system. Mass-spring systems are everywhere in engineering; your car, for instance, has a well-tuned mass-spring system that smooths the irregularities of the road for your comfort. Bridges are another mass-spring system – one where the mass(es) change irregularly, sometimes resulting in noticeable vibrations when a large truck passes by. Most of the time, these vibrations are well within the design limits the engineer has set.
Problems occur when the vibrations are at frequencies which elicit an unwanted response – resonance. Everything has some discrete frequencies at which it will naturally vibrate – these are called ‘modal frequencies,’ because each natural frequency produces a different shape (or ‘Mode’) of response (Figure 2). The first few Modes are simple shapes, getting more complex at higher frequencies. These modal frequencies become a problem when their response to an input frequency either results in a reinforcing response – higher total movement – or an amplified response to the input frequency. This is resonance.
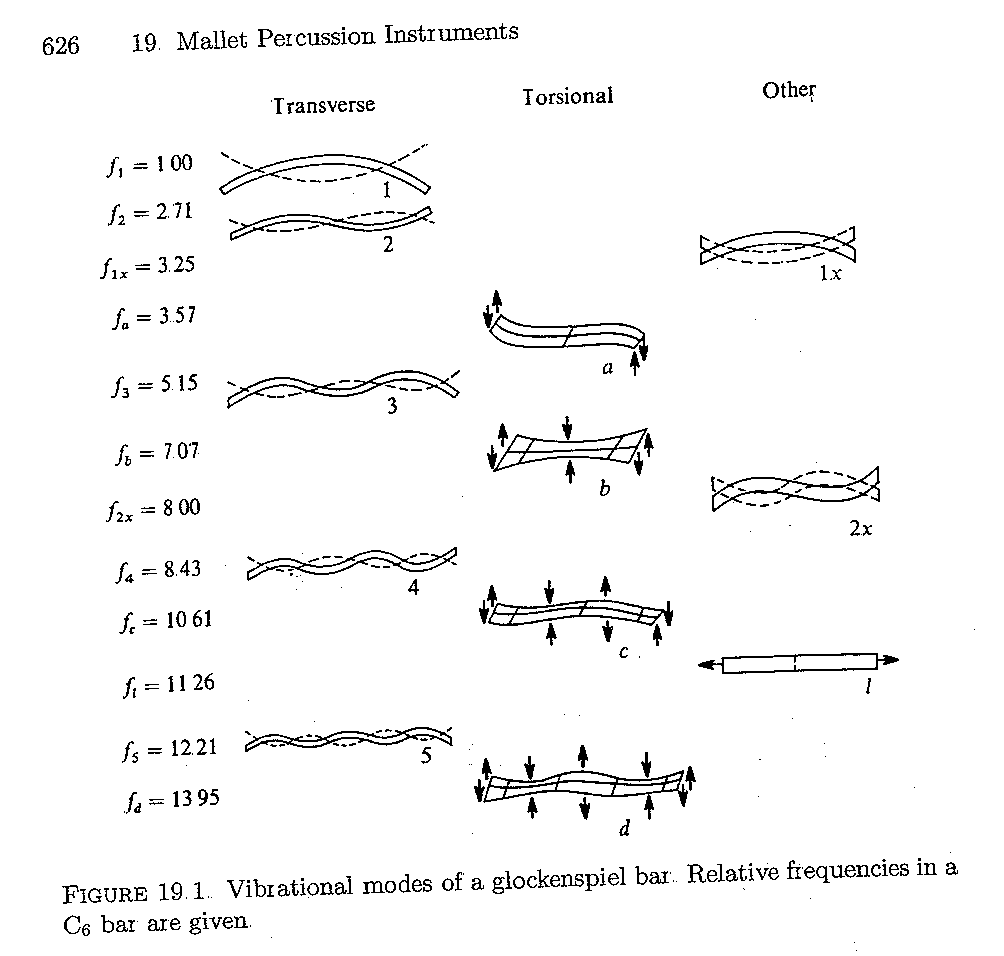
Normally, engineers try to ‘design out’ resonance. They’re not always successful – the Tacoma Narrows bridge – aka ‘Galloping Gertie’ – in 1940 was an example of misunderstood effects of a new design. More recently, the Millennium Footbridge in London opened on June 10th, 2000, closed for repairs on June 12th, 2000, due to an unpredicted feedback loop that caused pedestrians to walk at the same gait, inciting a lateral vibration in the bridge. Another common cause for unintended resonance is the addition of new or upgraded equipment which changes the mass of the original mass-spring system. Resonance in a system needs to be addressed before serious damage occurs – either to mounted equipment or the structure itself.
Like rotational imbalance, the first step a professional takes to determine detrimental structural resonance is to measure the accelerations. But unlike the rotational imbalance, the structure needs to have an input to excite the response. There are a couple of ways the professional can do this: one is to attach an oscillating shaker controllable at different speeds to excite the structure. Another is to place a long-term recording accelerometer package on the structure and monitor the response to random inputs over time. In either case, the time history from the accelerometers is again converted to a histogram and the professional looks for peaks in the response to indicate resonances.
Once the critical resonant frequencies are determined through measurement, actions can be taken to mitigate the issue. One way is to add damping – like the ‘shock absorbers’ (the English refer to them correctly as ‘dampers’) of your car. Damping reduces the restorative effect of the ‘springiness.’ Another way is to re-calculate the mass of the system – finding the new spring constant. That can be related then to the construction of the structure. Modifying the structure to increase the stiffness increases the first resonant frequency, the most likely dangerous resonance.
While ‘Galloping Gerties’ and wobbly footbridges are morbidly fascinating, that notoriety should be left in the textbooks. Look to your professional consulting engineer to smooth out resonance problems.
Other associated articles:
Part 1: A Balancing Act - Vibration Analysis of Machinery
About the Authors
Steven M. Lindholm, P.E., P.M.P. is a consulting engineer with our Oakland, CA office.
Mr. Lindholm provides consulting on inspection, evaluation, and design analysis of ship construction; stability; propulsion and auxiliaries condition assessment; ballast water treatment systems; vibrational analyses; and ship motion. He interprets and applies international (International Maritime Organization (IMO), class society, and flag state), United States Coast Guard (USCG/CFR), and regional regulations/guidelines to maritime casualties. Mr. Lindholm explores root cause investigation and analysis of mechanical damage to equipment, components, and materials, including fracture analysis and failure analysis, and prepares repair and replace cost estimates for marine, industrial, commercial, and residential systems.
You may contact either Steve at stevelindholm@edtengineers.com for your forensic engineering needs or (925) 674-8010
Learn about how EDT Forensic Engineering & Consulting approaches cause of damage, and forensic engineering by assigning a file today.